央廣網(wǎng)天津6月27日消息(記者周思楊)6月26日,記者從天津港保稅區(qū)企業(yè)海洋石油工程股份有限公司(以下簡稱“海油工程”)獲悉,位于天津港保稅區(qū)臨港區(qū)域的我國首個海洋油氣裝備制造“智能工廠”——海油工程天津智能化制造基地正式投產(chǎn),這標(biāo)志著我國海洋油氣裝備行業(yè)智能化轉(zhuǎn)型實現(xiàn)重大突破。
“智能工廠”總面積約57.5萬平方米,核心設(shè)施包括三大智能生產(chǎn)中心、七大輔助車間和八大總裝工位,設(shè)計年產(chǎn)能為8.4萬結(jié)構(gòu)噸,擁有總長1631米、適合大型海洋工程船舶及浮式生產(chǎn)儲卸油裝置(FPSO)停靠的優(yōu)質(zhì)碼頭資源。未來,該基地將重點發(fā)展油氣生產(chǎn)平臺及上部模塊、FPSO模塊、液化天然氣(LNG)模塊等高端海工產(chǎn)品,打造集海洋工程智能制造、油氣田運維智慧保障以及海工技術(shù)原始創(chuàng)新研發(fā)平臺等功能為一體的綜合性基地。據(jù)海油工程董事長于毅介紹,作為中央企業(yè)數(shù)字化轉(zhuǎn)型示范基地,海油工程天津智能化制造基地大量應(yīng)用5G、工業(yè)大數(shù)據(jù)、人工智能等先進技術(shù),通過分析和總結(jié)企業(yè)多年來在大型工程結(jié)構(gòu)物方面項目計劃、生產(chǎn)組織、車間執(zhí)行等技術(shù)和經(jīng)驗,實現(xiàn)從項目管控、車間建造到廠區(qū)管理的全流程智能化,為海洋油氣裝備行業(yè)提供可復(fù)制、可推廣的數(shù)字化智能化運營管理模式,推動企業(yè)運營管理積極向數(shù)字化轉(zhuǎn)型。
據(jù)悉,“智能工廠”主要包括以平面分段生產(chǎn)線、工藝管線生產(chǎn)線、自動化立體倉庫為主的生產(chǎn)系統(tǒng),以數(shù)字化智造管理系統(tǒng)、生產(chǎn)執(zhí)行系統(tǒng)、倉儲管理系統(tǒng)為主的軟件管理系統(tǒng),以信息采集系統(tǒng)、智能安防系統(tǒng)、動能監(jiān)測系統(tǒng)為主的場地支持系統(tǒng)和車間生產(chǎn)物流及材料配送系統(tǒng)等部分,通過智能制造技術(shù)應(yīng)用和各系統(tǒng)的精益集成,有力推動我國海洋裝備制造從傳統(tǒng)“人力工廠”邁向現(xiàn)代化“智能工廠”。
此外,“智能工廠”應(yīng)用自動切割、自動打磨、智能組對、智能焊接、智能倉儲等先進智能生產(chǎn)設(shè)備400余臺套,實現(xiàn)從材料入場到劃線、組對、打磨、焊接等車間預(yù)制流程的智能化,板材自動切割率達90%,甲板片自動焊接率達70%,總體生產(chǎn)效率較傳統(tǒng)模式可提升20%以上,成本控制和質(zhì)量安全管理水平大幅增強。“‘智能工廠’不僅大大減少了人工投入,而且通過智能設(shè)備控制輸出工藝參數(shù),避免人為因素產(chǎn)生的質(zhì)量隱患,提升工藝的同時保障人員施工安全。”海油工程天津建造分公司結(jié)構(gòu)預(yù)制車間高級技師耿孝敏介紹說。
據(jù)了解,傳統(tǒng)海洋油氣裝備制造屬于勞動密集型產(chǎn)業(yè),具有產(chǎn)品類型多、制造工序長、定制化比例大、標(biāo)準(zhǔn)化程度低等顯著特點,各生產(chǎn)環(huán)節(jié)的數(shù)據(jù)碎片化現(xiàn)象嚴重,實現(xiàn)數(shù)字化智能化難度極大,成為制約行業(yè)質(zhì)量效率提升的重要瓶頸。為此,海油工程組建200多人核心技術(shù)團隊,聯(lián)合國內(nèi)知名高校和科研機構(gòu),統(tǒng)籌國內(nèi)外優(yōu)質(zhì)資源,攻克智能化排產(chǎn)、智能定位組對、自動切割焊接、智能倉儲等智能制造關(guān)鍵技術(shù)難題,創(chuàng)新應(yīng)用“海洋油氣裝備大規(guī)模機器人焊接”等10項國內(nèi)“行業(yè)首次”先進技術(shù),實現(xiàn)海洋油氣裝備制造工藝管理數(shù)字化、生產(chǎn)任務(wù)工單化、生產(chǎn)設(shè)備自動化和生產(chǎn)過程可視化,填補我國海洋油氣裝備數(shù)字化、智能化制造領(lǐng)域的多項技術(shù)空白。
海油工程天津智能化制造基地投產(chǎn),是近年來中國海油積極踐行“四個革命、一個合作”能源安全新戰(zhàn)略、加快推進數(shù)字化轉(zhuǎn)型和綠色低碳發(fā)展取得的重要里程碑成果。下一步,中國海油將緊緊圍繞“1534”總體發(fā)展思路,持續(xù)加強原創(chuàng)性、引領(lǐng)性科技攻關(guān),大力提升海洋油氣裝備制造能力,把裝備制造牢牢抓在自己手里,努力為推動天津港保稅區(qū)乃至天津市海工裝備產(chǎn)業(yè)高質(zhì)量發(fā)展貢獻力量,全力為我國海洋科技實現(xiàn)高水平自立自強、保障國家能源安全、建設(shè)海洋強國打造強勁引擎。
轉(zhuǎn)載申請事宜以及報告非法侵權(quán)行為,請聯(lián)系我們:010-56807194
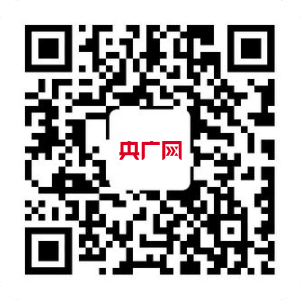
關(guān)注精彩內(nèi)容